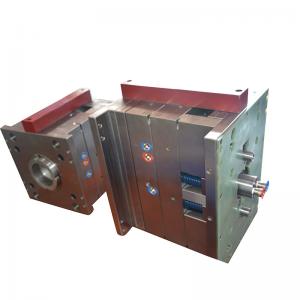
Add to Cart
1000 Shots 2 Cavity P20 H13 Electrical Plastic Molding
Product Details Description
Plastic Materials | H13, 2344, P20, 2311, Starvax 420, 236,S136, 2312, 2379, 2316, 2083, Nak80, 2767 ...etc. |
Standard | DME/HASCO standard |
Quality system | RoSH and SGS standard |
Feature | Non marking,non flash and non shrinkage |
Package | Standard exported Wooden box packed, Fumigation process(upon required) |
Mold Building Lead Time | T1, 30-50 days after the mold 3D approved, depends on different mold structure |
Mould Base | Hasco Standard, European Standard, World Standard |
Mould Base Material | LKM, FUTA, HASCO, DME,...etc. Or as per Customer's Requirment. |
Surface Finish | Texture(MT standard), High gloss polishing |
Cavity/Core Steel | P20, 2311, H13, 2344, Starvax 420, 236,S136, 2312, 2379, 2316, 2083, Nak80, 2767 ...etc. |
Cavity number | Single/multi cavity |
Hot/ Cold Runner | HUSKY, INCOE, YDDO, HASCO, DME, MoldMaster, Masterflow, Mastip,...etc. |
Mould Life | 1,000, 300,000 to 1,000,000 Shots. (According to your requirement.) |
Design & Program Softwares | CAD, CAM, CAE, Pro-E, UG, Soild works, Moldflow, CATIA....etc. |
Equipments | High speed CNC, Standard CNC, EDM, Wire Cutting, WEDM, Grinder, Plastic Injection Molding Machine for trial out mold from 50-1300T available. |
KYE Mould Technology Limited specialize in mold design, manufacture and product assembly since 2009. During the past decades, we served customers from worldwide by offering sustaining quality products and value-added services to help achieve customers’ success. Our professional industry knowledge, problem-shot experience, fast reaction services and low cost solutions strengthen customers’ competence in both end market acknowledgement and competitions.
We help you realize an idea to real product.
- Product idea viability check
- Product engineering verification
- Engineering design
- Prototype
- Tooling and molding
- Order production
- Assembly and packaging
- Logistics and shipping
Manufacture Capabilities
1. New project/design development assistance, base on customer’s samples or design drawing;
2. When the customer encounter bottleneck, give them some technical assistance;
3. Help the customer complete the 3D design drawing;
4. Simulate the effect of the product by simulation software and offer the simulation report;
5. Test Mold: Test Mold and Sample Making;
6. Delivery Mold: Delivery to Customer;
7. Product Making;
8. After service: After Sale Information Communication.
RAQ
Q1: Does your company make mold by yourself?
A: Yes, we have our owned mold workshop around 2,000 square meters including mold and molding.
Q2: What is the software you use for design and mold making?
A: We usually use UG, PROE, CAD, CAD/ProE/UG/SOLIDWORKS for mold 2D and 3D design.
Q: How you do the quality control?
A: we have system quality control process
1). Materials inspection by IQC;
2). The first sample inspected by QC, QC will do over check as per the parameters list and critical dimensions requested by customers, to decide if it can go ahead for production;
3). During processing, our IPQC will check the injection molded parts every 2 hours, ensure no any rejects;
4). FQC will check the products before sending to the warehouse;
5). 100% inspected by OQC before shipping out.
Q: How to pack the moulds and products?
A:
1). For moulds, we will be coated one-layer anti-rust oil first,and then also will be covered thin films on the mould, finally pack into fumigation wooden case.
2). And as to products, we will pack into standard export cartons or as per customer’s request to pack.